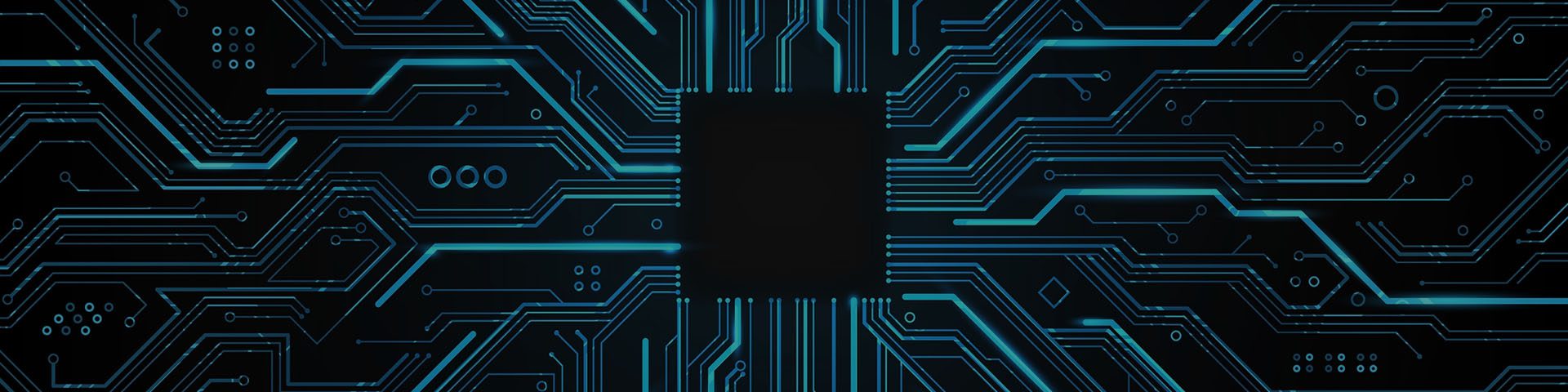
覆晶封裝
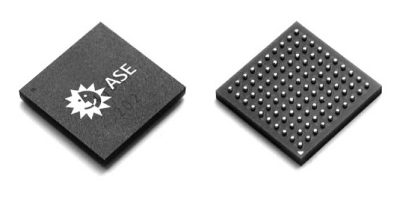
Flip chip derived its name from the method of flipping over the chip to connect with the substrate or leadframe. Unlike conventional interconnection through wire bonding, flip chip uses solder or gold bumps. Therefore, the I/O pads can be distributed all over the surface of the chip and not only on the peripheral region. The chip size can be shrunk and the circuit path, optimized. Another advantage of flip chip is the absence of bonding wire reducing signal inductance.
An essential process for flip chip packaging is wafer bumping. Wafer bumping is an advanced packaging technique where ‘bumps’ or ‘balls’ made of solder are formed on the wafers before being diced into individual chips. ASE has invested significantly in the research and development as well as in equipment for wafer bumping. It has the capacity to bump 6-inch, 8-inch and 12-inch wafers.
Benefits of Flip Chip
-
Shorter assembly cycle timeAll the bonding for flip chip packages is completed in one process.
-
Higher signal density & smaller die sizeArea array pad layout increases I/O density. Also, based on the same number of I/Os, the size of the die can be significantly shrunk.
- Good electrical performanceShorter path between die and substrate improves the electrical performance.
-
Direct thermal dissipation pathExternal heat sink can be directly added to the chip to remove the heat.
-
Lower packaging profileAbsence of wire and molding allows flip chip packages to feature lower profiles.
Capabilities
ASE offers several BGA packages using flip chip technology. There are:
I/O | Package Size(mm) | Substate | Ball Pitch(mm) | |
---|---|---|---|---|
CCSP | 16 ~ 200 | 4x4 ~ 14.0x22.0 | 2/4 Layer Laminate | 0.5 ~ 1.00 |
Ceramic FCBGA/PGA | < 1556 | 27x27 ~ 49.5x49.5 | Ceramic | 0.8 ~ 1.27 |
FCGBA | 100 ~ 1521 | 27x27 ~ 40.0x40.0 | 2/4 Laminate, 4-8 Layer Build-up |
1.0/1.27 |
HFCGBA | 256 ~ 2401 | 12x12 ~ 52.5x52.5 | 4-8 Layer Build-up | 1.0/1.27 |
The thickness and the available ball count of flip chip packages are mostly customized. ASE provides several options for enhancing the performance of flip chip packages. They are:
Overall molding (for FCCSP)
The molding is used to protect the chip, substitute underfill for lower cost and improve the thermal performance and 2nd level reliability.
Heat spreader (for FCBGA)
The heat spreader provides direct heat conduction by adhering to the rear side of the silicon chip. This method provides 6~8W of thermal dissipation under natural convection.
ASE Flip Chip Packaging Offerings
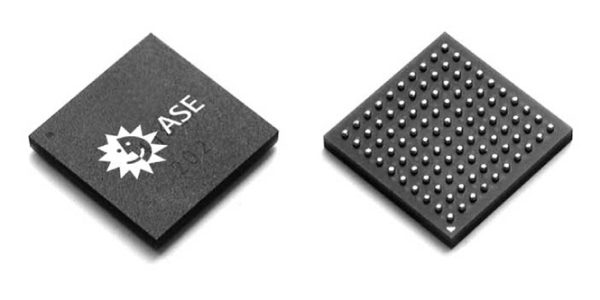
FCCSP (Flip Chip Chip Scale Package) offers chip scale capacity for I/Os around 200 or less. FCCSP provides better protection for chip and better solder joint reliability compared with direct chip attach (DCA) or chip on board (COB). FCCSP is more superior to known good die (KGD) in low-cost test and burn-in, and performs comparable electrical function with KGD. FCCSP features thin and small profile, and lightweight packages.
Applications
Consumer
- Camcorders
- Digital Camera
- DVD
Computer
- Voltage Regulators
- High-speed Memory
- Card
- PC Peripherals
Telecommunication
- Pagers
- Cellular Handsets
- GPS
Features
BGA is suitable for high-power and high-speed ICs requiring superb electrical and thermal enhancement.
- Thinner Profile: “Wafer Thinning” capability (down to 6~8 mils) to support packages thinner than 1.0 mm
- Substrate: 2-layer BT laminate substrate is used to reduce overall package cost
- Improved Performance: Thin core (100um) substrate & via-on-pad design can be adopted to achieve better electrical performance
- Robust Structure: Over-molded process can enhance throughput, component and board level reliability
- NSMD with OSP C4 pad: Low-cost solutions for electric interconnect between solder bump and substrate