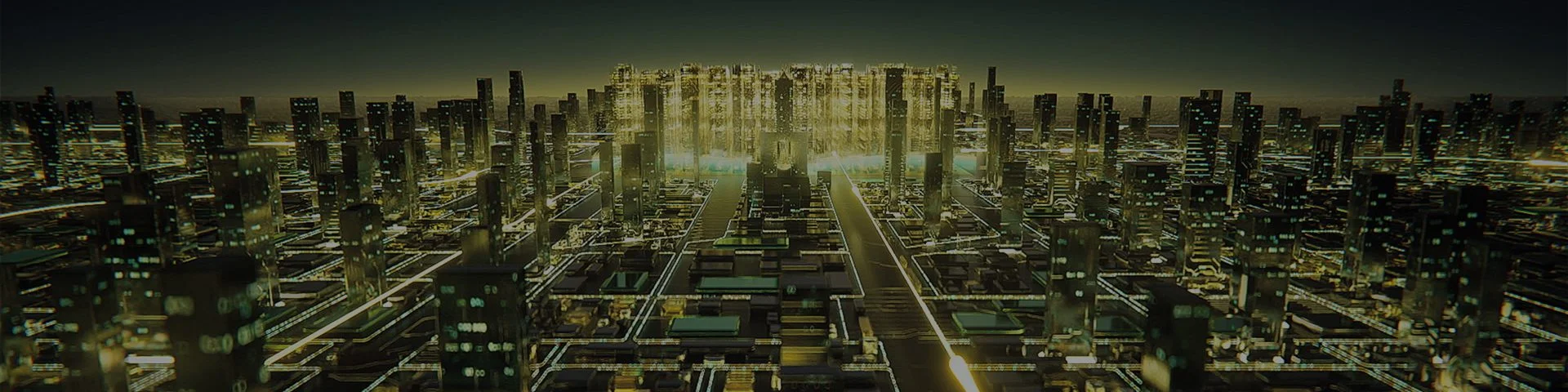
Company Info
Who We Are and What We Do
All around us, digital transformation is changing the way PEOPLE live, work, play and communicate. As a leading provider of semiconductor packaging and test services, ASE is playing a significant role in the development of the world’s most innovative electronics. Our technologies have also enabled our customers to create cutting edge products that deliver superior performance, power, speed and connectivity.
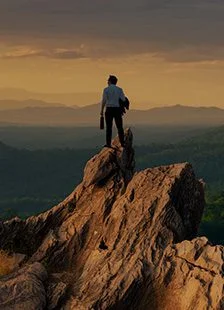
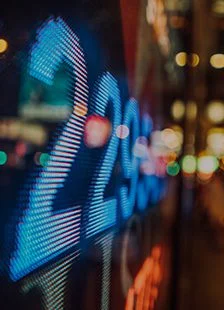
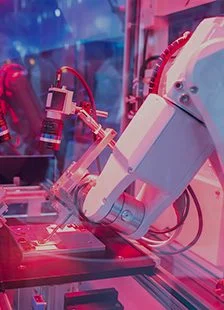
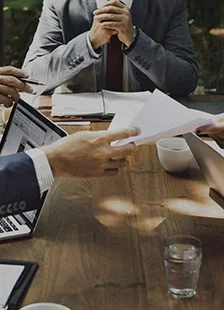
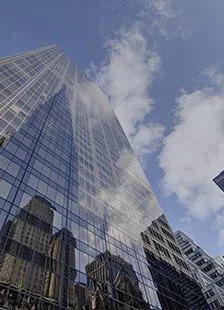
We Do So Much More
ASE is a primary architect of Heterogeneous Integration (HI) - the technology that integrates separately manufactured components into a higher level assembly (System-in-Package or SiP) that in the aggregate provides enhanced functionality and improved operational characteristics.
HI is now the key technology in the advancement of integrated systems for greater intelligence and connectivity, higher bandwidth and performance, and lower latency and power per function, all at a more manageable cost. To learn more about ASE Heterogeneous Integration click here and SiP click here.
Market shifts in customer requirements as well as the advent of 5G wireless technologies have given rise to smart manufacturing and the acceleration of Industry 4.0 at ASE. Smart Factories represent the future of our industry and are an integral part of ASE’s business operations. Our strategy is to leverage on AI, Big Data and Smart Automation to achieve full digital transformation. We are moving ahead of our time by harnessing the power of smart manufacturing to increase productivity, add more value to the supply chain and strive for near perfection.

We Are Building a Better World
Technology can make a better world and this belief has fueled our ambition to lead the industry in corporate sustainability through innovation, social, economic and environmental stewardship. We are focused on implementing robust policies that combat climate change, advance green technologies and manufacturing, promote a strong economy and serve public interests. In December 2022, we emerged as the only global enterprise to have successfully achieved the best overall performance on the Dow Jones Sustainability Indices - Semiconductors and Semiconductor Equipment Industry Group for seven consecutive years. ASE has also been on the CDP’s annual list for Climate Leadership for seven years’ standing since 2016, and Water Security A List since 2020. To learn more about ASE Corporate Sustainability, click here.
Premier IC Manufacturing Services
Automation, heterogeneous integration in machine and production systems, and heterogeneous integration in systems-in-package (SiP) are 3 major forces driving smart factories and digital transformation at ASE. Our strong foundation in automation coupled with the successful integration of our supply chain in the use of digital technologies have increased productivity and cost efficiencies, improved quality control and enable real time responsiveness to customer demands.
To learn more about Smart Manufacturing/Industry 4.0, please visit.

We are involved in many stages of the semiconductor manufacturing process - front-end engineering test, wafer probing, IC package design, substrate design and manufacturing, IC packaging (assembly), final test as well as module, board assembly and test in collaboration with our sister company, USI.
To learn more about Semiconductor Supply Chain, please visit.

Services offered by ASE
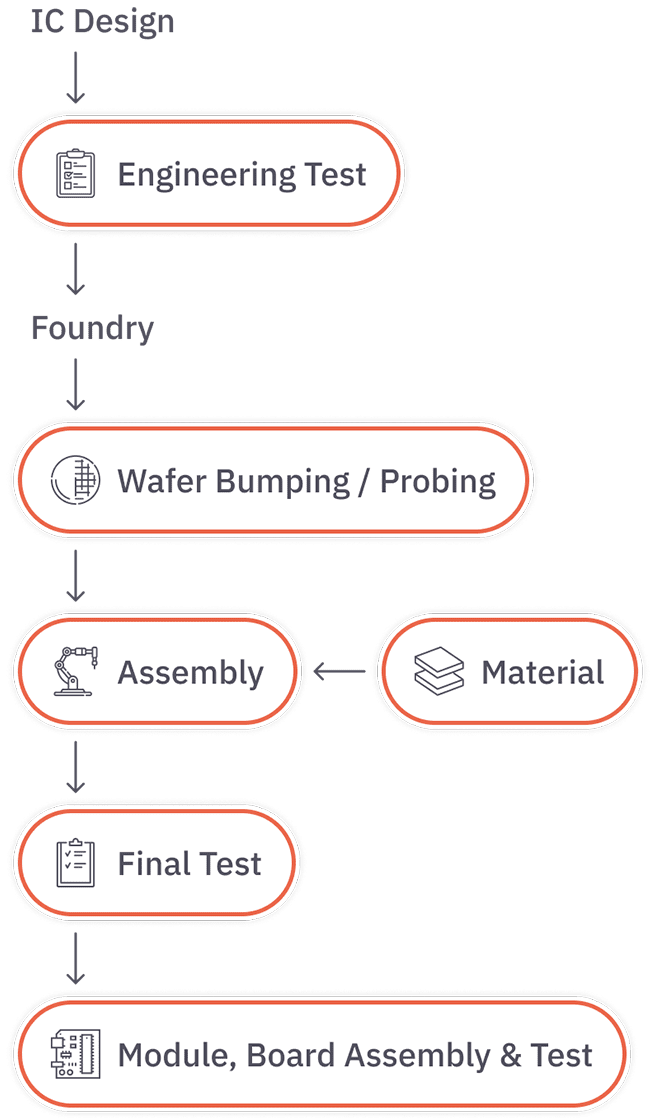