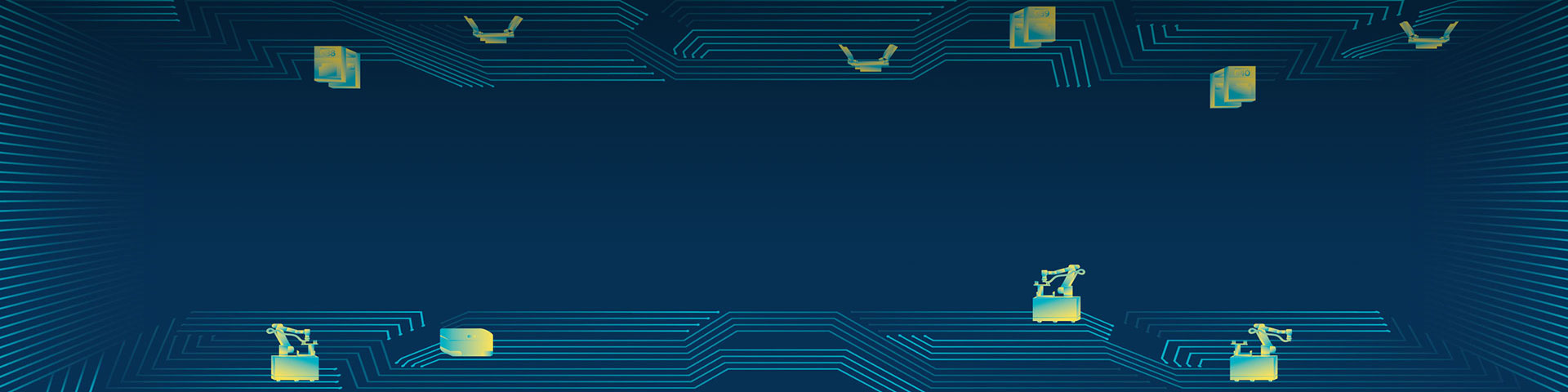
Smart Manufacturing

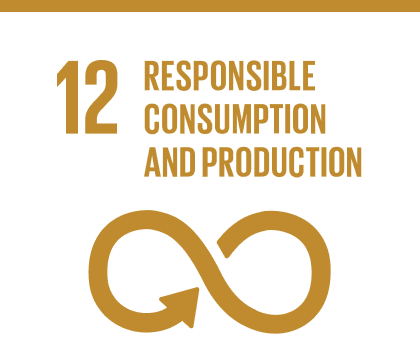
With the increasing complexity of the global business environment that is characterized by many factors including climate change, companies continue to face unprecedented challenges in their business operations. ASE is accelerating its adoption of smart manufacturing technologies to increase the efficiency of its equipment and productivity, as well as the use of smart technology to optimize energy consumption and savings. In line with the company’s vision of building advanced and robust smart factories, ASE established the CIM Committee in 2011 to drive digital transformation and the building of smart factories that are fully automated including several lights-out factories. Today, ASE operates a total of 46 lights-out factories.
Completed 46 lights-out factories in operation
1st OSAT factory inducted into the WEF Global Lighthouse Network
Trained and equipped more than 700 engineers on AI and automation

Smart Factory and Digital Transformation
ASE is collaborating with the best-in-class industry players to chart the course of the next generation in Smart Factory that will enable the digital transformation of factory processes that are highly secured, reliable and sustainable.

Number of ASE Smart Factories
Beyond Innovation
Industry Associations & Research Institutes
Co-chair of Smart Manufacturing Committee at SEMI
Deputy convenor of the Intelligent Automation Committee, Taiwan Printed Circuit Association (TPCA)
Automation technology collaboration with Institute for Information Industry (III), Industrial Technology Research Institute (ITRI), Metal Industries Research &Development Center (MIRDC)
Scholarships and Internship Programs
National Cheng Kung University,
National Sun Yat-sen University,
National University of Kaohsiung,
National Kaohsiung University of Science and Technology,
I-Shou University,
Southern Taiwan University of Science and Technology,
and Cheng Shiu University
Taiwan Automation Suppliers
Software solutions, Internet of Things sensors/controllers, automated transport systems, automated guided vehicles, robotic arms, etc.
Academic Research Units
60+ industry-academic projects, involving 30 professors and 60 graduate students
Value Chain Influence
- Local procurement promotes economic development
- Cultivate local automation suppliers and create corresponding job opportunities
- Improve human resource value, cultivate more than 700 automation and AI-related professionals
- Transform digital manufacturing and reducing overtime
- Build a safe production process to avoid workplace injuries
- Improve production efficiency, product quality and output
- Assist customers in product innovation and applications for a sustainable future