
Blog
Innovation and Collaboration in Power Module Packaging: A Thermal Perspective
Thomas Wang - Director, Corporate R&D
Power modules are the foundation of modern electrical systems, especially within electric vehicles (xEVs), industrial motor applications, and renewable energy solutions such as wind and solar power. As the demand for more power in smaller and lighter systems grows, managing heat dissipation has become a major challenge, as the thermal energy from high current flows can lead to reliability issues. Effective thermal management solutions are essential.
At ASE, we recognize that addressing thermal challenges is paramount to unlocking the full potential of power modules. To tackle these challenges, we can approach thermal management from three key perspectives: reducing thermal sources, minimizing thermal interfaces, and lowering thermal resistance. Each approach plays a vital role in enhancing performance and reliability of power modules.
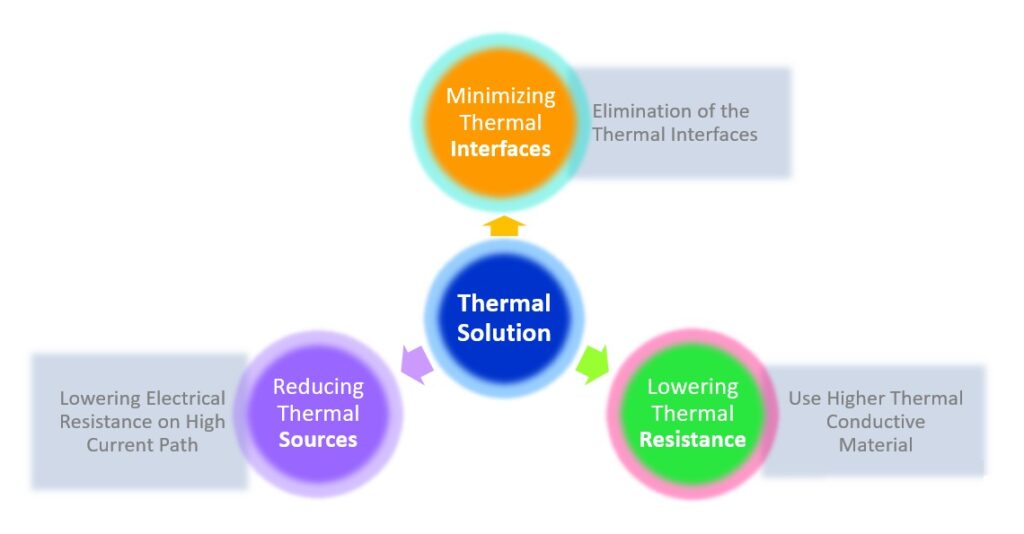
Reducing Thermal Sources
The main source of heat in power modules arises from the significant current that flows through different components, such as terminal connections, internal connections, die attach, and the power die itself. To mitigate this, we can employ several strategies:
- Thinner Die Design: By reducing the thickness of the power die through backside grinding and then applying metal to the back side again, we can minimize the switch ON resistance, which in turn reduces heat generation.
- Advanced Die Attach Materials: Transitioning from traditional solder pastes to silver or copper pastes, combined with pressure sintering methods, can significantly decrease electrical resistance and improve thermal conductivity.
- Improved Package Internal Connections: Instead of traditional aluminum wedge bond, utilizing aluminum ribbon bonds, copper clip solder connections, or heavy copper wire bonds can significantly reduce the heat generated by the flow of current. In addition, reducing thermal buildup.
- Optimized terminal connections: For the terminal design, a thicker and shorter configuration is preferable. Utilizing metal welding instead of traditional soldering.
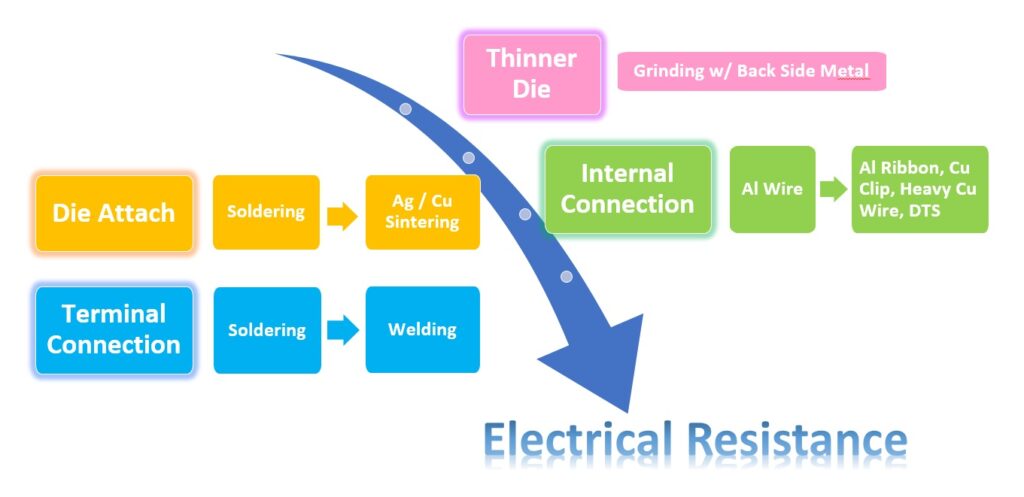
Minimizing Thermal Interfaces
The thermal dissipation efficiency in power modules is significantly hindered by the multiple thermal interfaces that exist between the primary heat source, namely the power semiconductor, and the heat sink. In a conventional power module, illustrated in the left structure of the figure below, the power die is first soldered to a ceramic substrate, which is then soldered to a base plate, and finally attached to a heat sink cooler. By innovating the design of power module structure, we can reduce these interfaces:
- Structured Baseplate Design: The initial approach for minimizing thermal interfaces is to employ a base plate with pin fins that serves as a replacement for both the conventional base plate and the pin-fin heat sink, as shown in the middle structure of the figure below.
- Integrated Substrate Design: By integrating the ceramic substrate’s bottom copper layer with a pin-finned base plate, as depicted in the right structure of the figure below, we can further eliminate unnecessary and solder interfaces, allowing for a more direct thermal dissipation path.
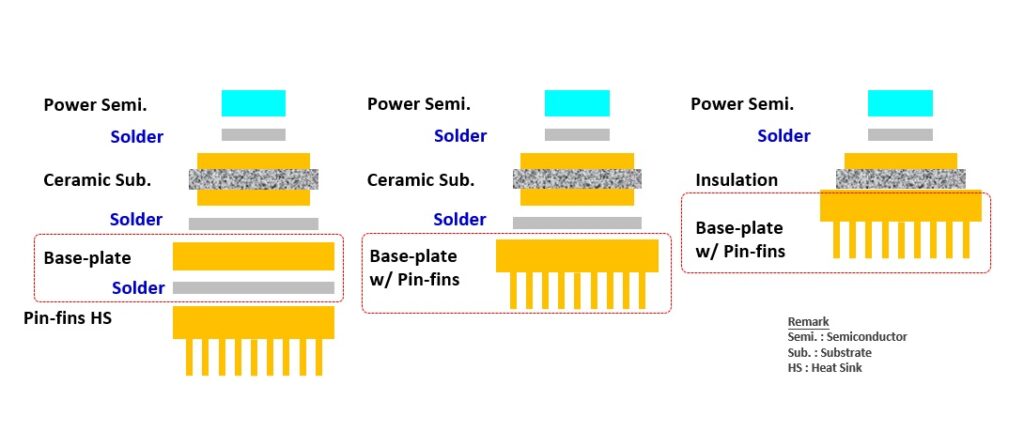
Lowering Thermal Resistance
The choice of materials plays a crucial role in thermal management. For instance, replacing aluminum oxide with silicon nitride or aluminum nitride as insulation layers of ceramic substrates can significantly enhance thermal conductivity.
ASE’s Commitment to High Volume Manufacturing
At ASE, we are at the forefront of high-volume manufacturing processes tailored for power modules. As illustrated below, our capabilities encompass die bonding, wire bonding, substrate attachment, case assembly, and advanced soldering techniques, including formic acid reflow and metal welding. These processes have been meticulously developed to ensure reliability and efficiency.
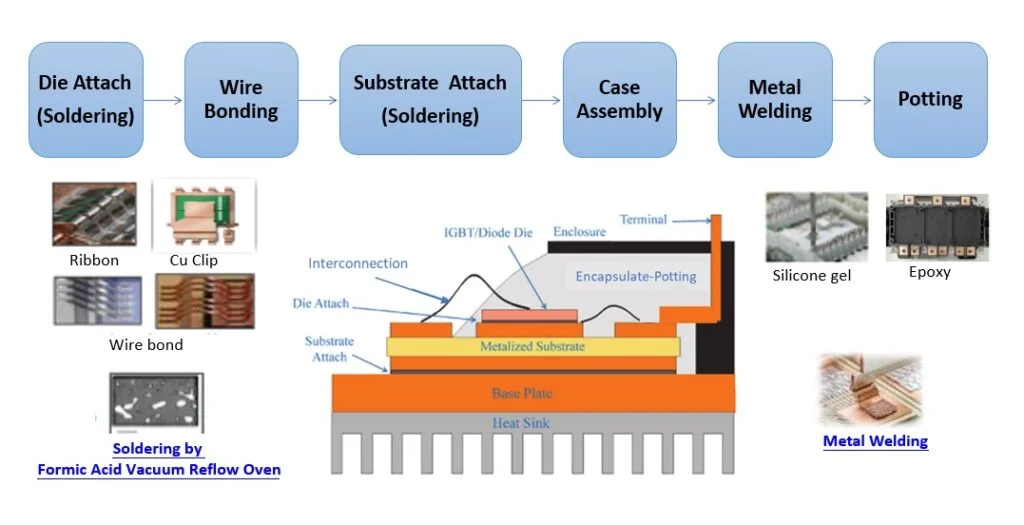
Collaborative Innovation for Future Growth
The power module market is projected to grow to $14.8 billion by 2028, with a compound annual growth rate (CAGR) of 12.8%, primarily driven by the surge in electric vehicles (Source: Yole_Status of the Power Module Packaging Industry 2023). At ASE, we recognize that success in this competitive landscape depends on strong collaboration. We actively engage with our customers to co-develop solutions tailored to their unique thermal and performance requirements.
Our comprehensive capabilities in mechanical design, thermal analysis, and reliability simulation allow us to collaborate closely with clients, ensuring that our power modules not only meet but exceed industry standards. By leveraging advanced simulation techniques, we can optimize power distribution networks, conduct thermal simulations, and assess reliability under various conditions.
Conclusion
Innovation and collaboration are the driving forces behind the evolution of power module packaging. At ASE, we are dedicated to pioneering thermal solutions that not only enhance performance but also ensure reliability in high-volume manufacturing. By fostering partnerships and embracing cutting-edge technologies, we are poised to lead the way in the power module industry, ready to meet the challenges of tomorrow.
Join us on this journey as we continue to innovate and collaborate, shaping the future of power electronics for a sustainable and efficient world. Together, we can unlock new possibilities and drive the next wave of technological advancements in power module packaging.